As an intern, I have been unsure about my position - though I am certain it is at the bottom. Still, it is pretty hard to know where to you stand. Some days the intern will feel as though he can do absolutely nothing right - but it gets better. Just remember that you are here to learn - and try not to be shy. It is good to know how to keep your eyes and ears open and your mouth shut - but nothing will be handed to you at ULAE in terms of learning. I mostly have just hovered over the printers and picked their brains - asked questions about everything they are doing, to which some printers respond much better than others. Don't feel like a nuisance - you are one - but don't let it get to you. Besides the alternative is running errands and doing office work. Since I've been here, I have helped the printers with a number of things, including helping with a Rosa Loy Litho edition. This has included some menial press operation tasks, wiping plates and cleaning rollers. I feel good about this work because it saves the printer a whole lot of time and elbow grease. On the Loy edition we ran abut 80 sheets, which means a lot of work on ach individual sheet at mant different stages. I started out by tearing paper, then cleaning plates, and wiping the litho block on the stone press. I was then assigned to tear paper AGAIN, which is the last step before curating. I will go into a bit more detail about litho and etching in later blogs - but suffice it to say, just by making myself available I have learned a whole lot through proximity and practice.
Sorry these are not chronological by any means -- damn technology!
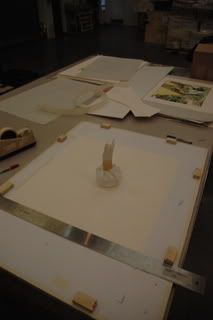
To tear down paper for the finished prints, a tear down block is constructed to ensure that every sheet of the edition is exactly the same. The borders round the image must be the same for every sheet. The paper is held in place with pins in the registration marks, and then weighted so the paper doesn't move. It seems like a male job - but these are very expensive sheets of paper, so it must be done right.
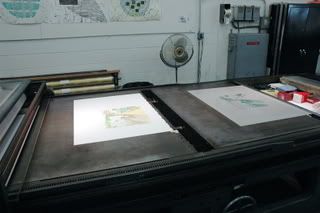
The offset press is an essential element of the editioning process. It allows an unlimited number of prints to be run in a very short amount of time. That doesn't make it easy - it is a high maintenance machine and there are many variables that can cause printing to be a nightmare if overlooked. The Rosa Loy prints were three base colors - so 80 sheets of paper run 3 times with a different plate - thats 240 runs, then black, run on the old litho press - which in itself took an entire workday, and we only got up to the 60th sheet. In between each run, registration must be checked - ink added or removed, blankets wetted, and routine trouble shooting. The printer must also make sure every print looks exactly the same in terms of color. You can see where an apprentice is a huge help.

Here is the whole edition prior to printing the black. Some editions are several hundred - and when you get into the Johns and Rauschenbergs, even more. Each sheet is worth a TON of money. Printers get printer's proofs, which are only saleable after the edition sells out.
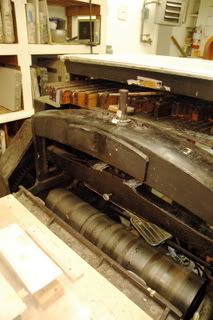
Here is a shot of the press at Skidmore. The surface of the sone must remain wet at all times during the printing process - so having someone to wet the stone is a neccesity. The registration setup took a little trouble shooting - but the printer eventually devised a very simple and efective system, and with two people, the last step of the editioning process went very smoothly - though it took about 8 hours of standing over the press.
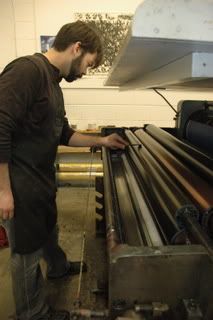
Jason (the man who taught me everything In know about Lithography) carefully adds ink into the rollers, which will even distribute and oscillate the ink so it prints completely flat. The printer must often rely on sight and intuition to add and remove ink or pressure so that all prints match the matchup proof, which has been aproved by the artist prior to editioning.
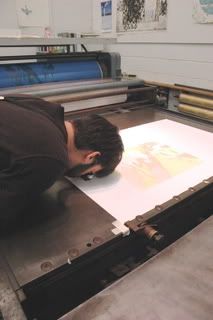
This is a very breif overveiw of my apprentice work with litho. Next week - what I've learned about etching.
No comments:
Post a Comment