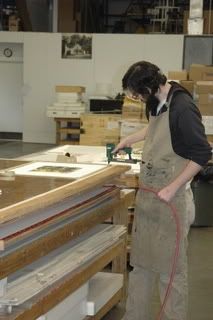
Ed, a printer from Norman, OK, staples a freshly printed Terry Winters to a wooden panel to ensure that is dries completely flat and even. Straps are used around the edges of the sheet to protect the surface, and the wood has a thick plastic sheet under it so the back of the sheet is not compromised either. These are very expensive prints, so great lengths are taken to ensure that they make it to the edition in pristine condition.
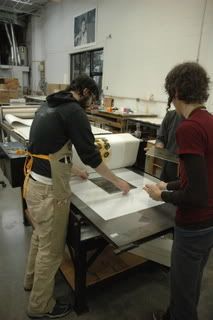
Ed lays a plate on the press for the last run on a Winters print. The prints are registered by ticks around the outer edge of the plate which line up with a grid on mylar. There were three prints in the particular edition - but the portfolio consists of ten different prints at 60 sheets each.
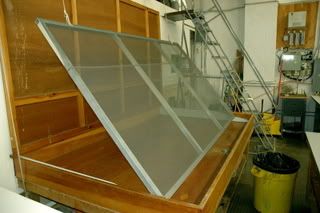
This is where paper gets soaked, and then drained when the screen is raised. It is then blotted before use. Damp paper draws more of the ink from the etched plate than a dry sheet.
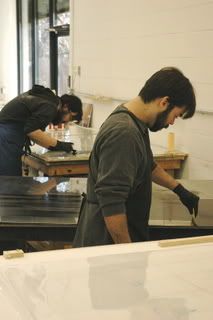
Ed and Jason ink an enormous Kiki Smith plate. The plate is set on a hotplate and ink is applied to it while warm, which helps the ink settle into the deeply bitten areas of the plate. Excess ink is then removed from undesired areas with tarletans, cotton wipes and a fine paper which picks up ink from the plate without removing it from etched areas. This process is done before every print is run.
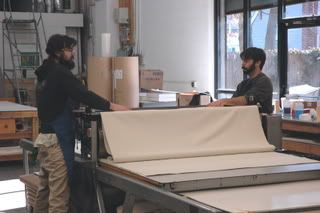
Here, a print is being run. This is truly a two man job - as the plate is very heavy and akward to move, and each printer must pull the wool blankets snug as the print runs underneath the roller, because any crumpling or creasing could be disasterous. I have spent many morings at the laundromat cleaning these blankets. (Incidentally, Planet Laundry is the place to go - an impressive facility as far as laundromats are concerned. Don't forget the Woolite!)
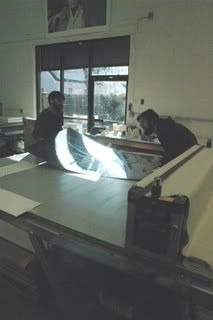
The printers move the plate from the hotplate to the press bed. Shiny!
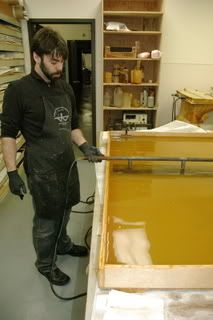
Before any printing begins, the plate undergoes a process called "Steel Facing." During which, the plate is fully immersed in rust filled water. The water is highly ionized, and highly conductive. While one end of the plate is connected to a power source (pictured below) a long steel pole, also charged is run across the surface of the plate. The pole never touches the plate, but the plate draws ionized steel particles to its surface during the several hundred passes it undergoes, and comes out coated in a very durable metal which will hold up to many more runs through the press that a plain copper plate. This is a painstaking process - but fortunately is only done before printing begins, unless the steelfacing begins to break down, in which case printing must be stopped, and the plate stripped and refaced, making everyone quite grumpy.
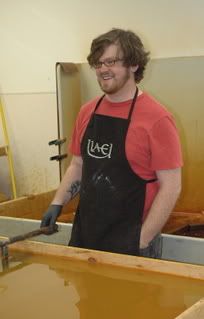
Do't let this image fool you. This really isn't very much fun.
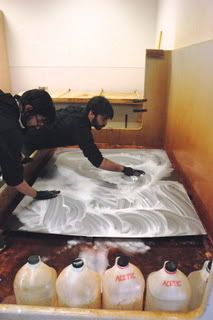
The plate must be washed with marble powder, ly and nitric acid to remove the existing steel facing, should a new face need to be applied.
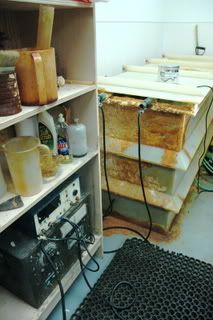
Here is the power source. The Kiki plates were to big for the facing tank you see in the back, so the flat bath was used. Were it a smaller plate, it would simply be suspended it the tank for a decided length of time, and the charged poles and hangers would do all the facing work.
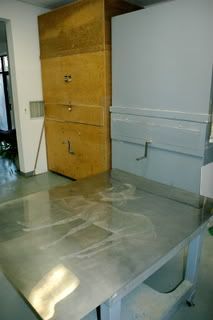
Here is the plate after steel facing, which would be printed from the following morning. You can see it apears silver, but that is really just a sheen of protective steel. When this plate was etched it still apeared copper. Behind it you see two large aquatint boxes - an area I hope to investigate while I'm here. Anyway - from the last two posts you can see tht simply making yourself available makes the days go by a lot faster. The more you hang out in the office, the errands you wil run. (You will still run errands.) Days where I am busy helping and learning make for a happy intern. And the more i have helped and shown enthusiasm, the more responsibilities I have been given, which feel really good.
1 comment:
Sooo...I'm pretty sure Kiki was working on that plate when I was there. A year ago!
Post a Comment